The Power Partners commitment to manufacture quality distribution transformers is backed by a series of transformer tests used to verify conformance to performance characteristics outlined in the latest revisions of ANSI C57.12.00 and ANSI C57.12.90. These identified tests are also part of the Quality System which is audited annually by an accredited third party auditor to the ISO Standards.
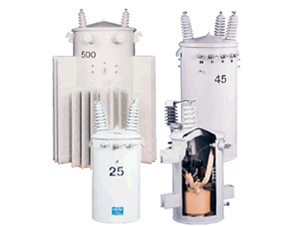
Testing
Factory tests are performed on a transformer to confirm that it is properly designed and constructed to carry rated load and that it will withstand the conditions it will be exposed to in service.
Each transformer manufactured by Power Partners must undergo a series of tests:
- Polarity, Phase-Relation, and Ratio
- Applied Voltage Test of the HV
- Applied Voltage Test of the LV
- Induced Voltage Test
- No-Load (Excitation) Loss and Excitation Current
- Circuit Breaker Test (for CSP transformers only)
- Impedance Voltage and Load Loss
- Full Wave Impulse
- Continuity Check
Test Facilities
The multi-station, automated test facilities are operated by process control computers. Required interaction with test floor personnel is minimal with the computers initiating and monitoring each test, and then analyzing the test results feedback. The computers are programmed to conduct tests according to ANSI standards, and according to the ratings of each transformer style, the test floor computers will initiate appropriate test setups, compare results with established ANSI standard limits, and determine acceptance for each tested unit.
The test results for each unit are recorded and stored on computer files for access and analysis.
Special Tests
Some tests are performed at the option of the customer.
Sound Testing
ANSI standards define the required sound levels for transformer but some customers specify reduced sound levels. The sound generated by a transformer is affected by the core geometry, flux density, tank design, and the quality of assembly of all the transformer components into a completed unit. Sound tests are made with the unit powered at 100% and 110% of rated voltage under no-load conditions.
Temperature Tests
Core losses and coil losses are the primary sources of heating within the transformer. Our transformers are guaranteed to have an average coil winding temperature of no more than 65 C rise over ambient air temperature when operated at rated voltage and load conditions. The temperature test is performed to determine the thermal characteristics of the transformer and to verify that they are within design limits.
Calibration
Test equipment is calibrated on a scheduled basis by trained technicians. Calibration records are maintained in accordance with the Quality System procedures. These are audited semi-annually by DNV in accordance with ISO.
Capabilities
Short Circuit Withstand Capabilities
Distribution transformers are subjected to external short circuits on the secondary side. Such external faults can develop on the service line, in the house wiring or in connected loads due to numerous environmental reasons. These faults can be line-to-ground, double line-to ground or line-to-line.
To meet these operating conditions, the American National Standard Institute (ANSI) has set standards concerning short circuit withstand capability. These standards require that distribution transformers shall be designed and constructed to withstand the mechanical and thermal stresses produced by these external short circuits.
The current standards relating to short circuit strength are ANSI C57.12.00 which sets the short circuit withstand requirements for distribution transformers and ANSI C57.12.90 which provides procedures for short circuit testing.
For distribution transformers, the magnitude of the short circuit current, the numbers of short-circuit tests and the duration of each short circuit test are defined by ANSI standards as follows.
A. Magnitude
Category | Single Phase kVA | Three Phase kVA | Capability* |
---|---|---|---|
I | 5-25 | 15-75 | 40 |
37.5-100 | 112.5-300 | 35 | |
167-500 | 500 | 25 | |
II | 750-2500 | 1/Z T** | |
* Base current (Symmetrical) per unit for all distribution transformers with secondary rated 600 V and below. ** The short circuit current will be limited by the transformer impedance only. |
B. Number of Tests
Each phase of the transformer shall be subjected to a total of six tests, four with symmetrical fault currents and two with asymmetrical fault currents.
C. Duration of Short Circuit Tests
When short circuit tests are performed the duration of each test shall be 0.25 s except that one test satisfying the symmetrical current requirement shall be made for a longer duration on distribution transformers. The duration of the long test in each case shall be as follows:
Category I:
T=1250/I2
Where T is the duration in seconds,
And I=Isc/IR=symmetrical short circuit current, in multiples of normal base current except I shall not exceed the maximum symmetrical current magnitudes listed in A.
Where Isc=IR/ZT=symmetrical short circuit current, in rms amperes
IR=rated current on the given tap connection, in rms amperes
ZT=transformer impedance on the given tap connection in per unit on the same apparent power base as IR
Category II:
T=1.0 second
Criteria of Satisfactory Performance
According to ANSI Standards a unit is considered to have passed the test if it passes a visual inspection and dielectric tests. Recommended additional checks include examination of wave shape of terminal voltage and current, leakage impedance measurement and excitation current test. (Refer to ANSI C57.12.90.)
The standard allows the following variations in the leakage impedance:
ZT (Per Units) Percentage Variation
0.0299 or less 22.5-500 (ZT)
0.0300 or more 7.5
ZT=per unit impedance of the transformer.