The Power Partners factory utilizes a paint finish process called “2CEC”, a trademark for a two-coat cathodic electrodeposition paint process. This new advanced coating technique maintains the structural integrity of transformers that are subjected to the long-term corrosive environments of coastal areas and industrial contaminants.
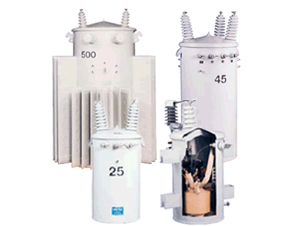
Process
Cathodic electrodeposition of paint occurs when direct current is applied to positively charged resin micelles dispersed in water. The resin micelles migrate toward the cathode (transformer tank) and are deposited in a process known as electrophoresis. As the process continues, the thickness of the deposit builds, resistance increases, and the film reaches a thickness limit. The most accessible areas are coated first, but as the resistance increases, less accessible areas coat, producing a highly uniform film build. Two-coat cathodic electrodeposition is the application of two coats of paint (epoxy primer/acrylic urethane topcoat).
Pretreatment
Prior to welding to the tank shell, stamped external hardware such as hanger brackets and lifting lugs are vibratory finished to remove burrs and insure a smooth radius edge to allow consistent edge coating.
An eight-stage dip process provides two cleaning steps completely remove lubricants and soils. A zinc phosphate coating is applied to enhance corrosion protection by providing tighter, more consistent coating than the typically used iron phosphate. The use of deionized water in the final rinse stages insures that the surface is free of salts and ions that could later provide sites for corrosion initiation. All pretreatment stages are immersion stages, which assures complete and total coverage.
The electrodeposition process assures complete and consistent coverage of the entire tank including complex shapes such as fins, hanger brackets, and lifting lugs.
The “2CEC” process allows us to optimize the performance of the primer and topcoat independently to maximize corrosion protection and ultraviolet light resistance while maintaining superior mechanical properties.
Paint process consistency is assured through automated paint feed and monitoring of a real time basis. Paint system operators monitor and audit the process.
Advantages
- Complete and uniform coverage of complex shapes, including edges and corners, hanger brackets, ground pads, and tank bottoms.
- Access into partially closed areas, such as inside the hanger brackets.
- High solids film eliminates sagging problems.
- Minimal organic solvent content.
ANSI C57.12.28 Performance Requirements
ANSI Standard C57.12.28 served as the benchmark for performance on the tests listed below. The test results clearly indicate the two-coat cathodic electrodeposition to be a leader in corrosion resistance, while maintaining excellent performance in all areas of the ANSI standard. “2CEC” passed all the tests listed here.
Salt Spray Test
Panels are scribed to bare metal and tested for 1000 hours in a 5% salt spray per ASTM B117-85E1 and evaluated per ASTM D1654-79A. Loss of adhesion from bare metal must not exceed more than 1/8″ from the scribe. Underfilm corrosion must not exceed more than 1/16″ from the scribe.
Crosshatch Adhesion Test
Panels are scribed to bare metal with a crosshatch pattern and tested per ASTM D3359-83. There must be 100% adhesion to the bare metal and between layers.
Humidity Test
Panels must be tested for 1000 hours in accordance with ASTM D2247-86A. There must be no blisters.
Impact Test
Test panels were impacted per ASTM D2794-84 at 160 in.- lbs. of impact. There must be not chipping of the paint on the impact side of the test panel.
Oil Resistance Test
Oil resistance testing is conducted at both 100°C and ambient for 72 hours. There must be no apparent changes, such as color shift, blisters, loss of hardness, or streaking.
Ultraviolet Accelerated Weathering Test
Test panels must be exposed for 500 hours in accordance with ASTM G53-84. Loss of gloss must not exceed 50% of the original gloss as described in ASTM D523-85E1.
Abrasion Resistance – Taber Abraser Test
The total coating system must be tested using a CS-10 wheel, 1000-gram weight, in accordance with ASTM D4060-84. The number of abrasion required to wear the coating through to the substrate must be at least 3000 cycles.
The ANSI C57.120.28 test results clearly indicate the two-coat cathodic electrodeposition is a leader in corrosion resistance while maintaining excellent performance in all areas of the ANSI standard. The two-coat cathodic electrodeposition maintains consistent, uniform paint coverage over the entire product, with no runs or sags, and offering a superior coating on distribution transformers.